Material Flow Planning: A Guide for Processing Facilities
Designing a facility around optimal material flow is one of the most impactful ways to improve operational efficiency, reduce waste, and increase throughput. In this article, we’ll explain what material flow planning is, how it benefits various types of processing operations, and what it takes to implement an effective system.
Drawing on Mobius’s expertise in facility optimization, automation, and production planning, we’ll also share practical strategies that apply broadly across industries such as food and beverage, health and wellness products, and agricultural and specialty processing.
Whether you’re managing a cannabis cultivation site, food processing, or a supplement packaging line, improving how materials move through your facility can lead to measurable improvements in productivity, product quality, and profitability.
What Is Material Flow Planning?
Material flow planning is the strategic process of designing how products move through a facility, from the delivery of raw inputs to final packaging, with the goal of keeping operations smooth, efficient, and logically connected.
By minimizing delays and unnecessary handling, good material flow planning supports higher throughput, more consistent quality, and better use of space and labor. Efficient handling can also help protect delicate compounds, especially in cannabis, where terpene preservation matters.
In cannabis facilities, this might mean mapping the movement of flower from bucking to trimming, then through sorting, drying, and packaging. For powdered supplement producers, it means optimizing how materials move between blending, encapsulating, bottling, and labeling. In mushroom farms or dried fruit facilities, the sequence might include harvesting, washing, milling, drying, grading, and packing, with each step flowing directly into the next.
Although the details vary from one industry to another, the underlying goal stays the same: design a system that allows materials to move smoothly from beginning to end, without doubling back or slowing down. Factors like shelf life, hygiene protocols, dust control, and product handling all influence how that system should be built, and why a one-size-fits-all layout rarely works.
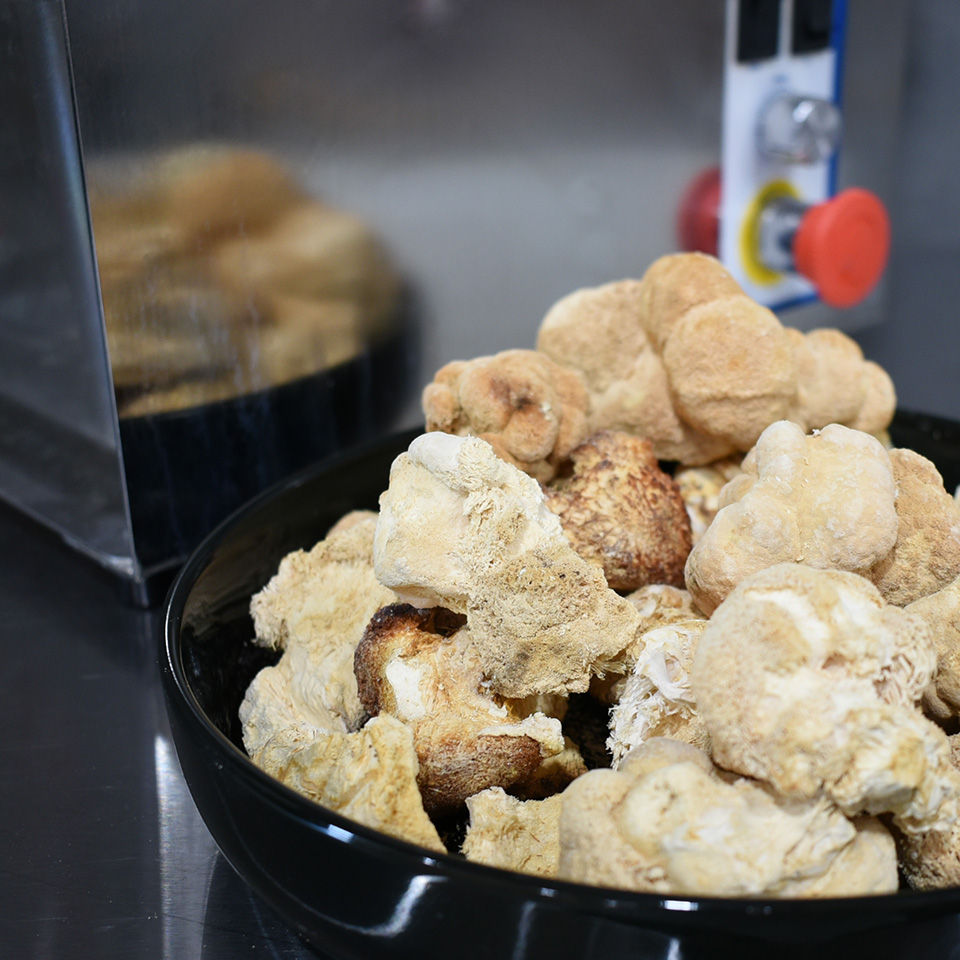
Material Flow Types
When planning material movement through a facility, it’s helpful to think in terms of two main categories: internal and external flow.
Internal Material Flow
Internal flow refers to how materials move within a single facility, from receiving raw goods and storing them to transferring items between processing zones and eventually into packaging.
Poor internal flow can lead to slowdowns, backtracking, and unnecessary handling. This not only wastes time but also increases the risk of cross-contamination or mistakes. In regulated environments that follow guidelines like GMP standards, such as cannabis, food, or cosmetics manufacturing, clearly defined pathways and separation between clean and raw zones are essential for maintaining compliance and product quality.
External Material Flow
External, or interplant, material flow refers to transferring materials between separate sites. For example, moving biomass from a grow facility to a processor, or shipping finished goods to a distribution center.
For multi-state operators (MSOs), this gets more complex. State-by-state differences in transport and storage rules demand tight coordination across locations. The focus isn’t just on how far products are going, but how they’re handled and documented along the way.
Regardless of location, well-managed flow reduces touchpoints, limits handling, and keeps materials aligned with the production schedule and broader supply chain — all of which require input from logistics teams and planners early in the process.
Why Is Material Flow Planning Important?
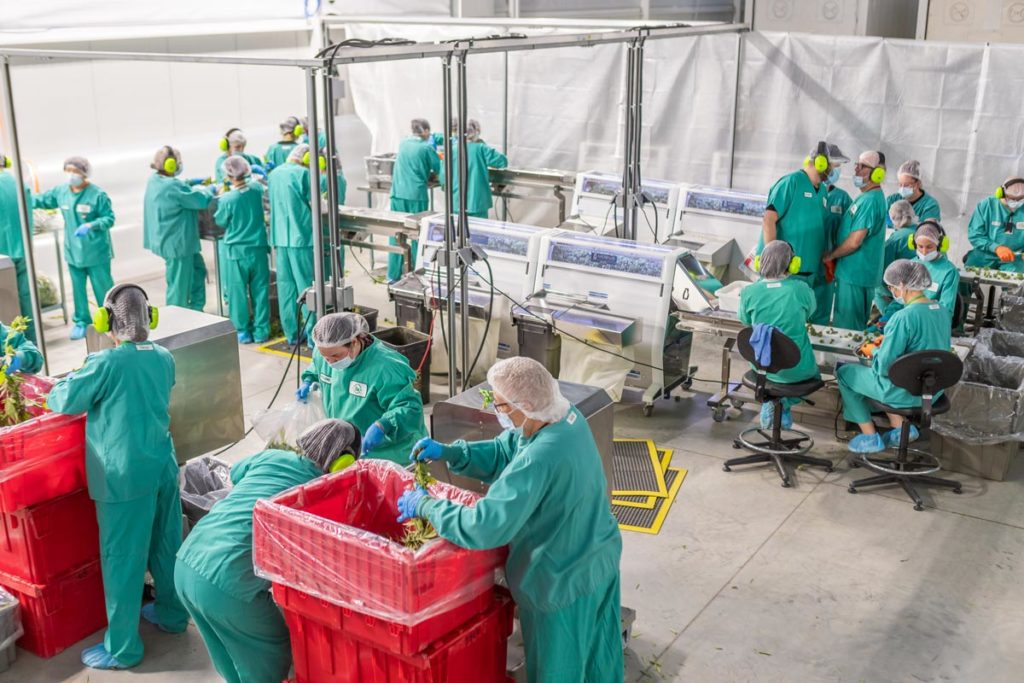
A well-planned material flow system creates a more resilient, efficient, and profitable operation. It also strengthens the supply chain by eliminating inefficiencies, such as bottlenecks at trimming stations or weighing points, and replacing them with intentional, linear movement paths that are easier to manage, automate, and maintain.
The benefits of material flow planning include:
- Increased throughput: Proper planning can eliminate delays between processing stages, allowing materials to move efficiently from one area to the next without unnecessary stops or slowdowns.
- Improved product consistency: When transitions are clearly defined and well-organized, it becomes easier to maintain the same quality standards from batch to batch.
- Reduced risk of contamination: Separating raw material handling areas from finished goods zones through thoughtful layout design helps maintain cleanliness and supports compliance with industry regulations.
- Lower labor costs: By reducing manual handling and creating logical, task-specific workstations, facilities can streamline labor needs and operate with fewer unnecessary touchpoints.
- Higher yield and less waste: Efficient flow paths minimize the risk of overhandling, which is especially important when working with fragile or easily degraded materials.
- Shorter time to market: A well-structured process reduces turnaround time, enabling faster order fulfillment and improving customer satisfaction.
- Scalability: When material flow is built with flexibility in mind, it’s easier to expand operations, introduce new product lines, or adapt to increased demand without reworking the entire facility.
When applied correctly, material flow optimization supports meaningful process improvement by enhancing the movement of goods, and the communication, coordination, and accountability of staff and systems throughout the entire production process.
Steps to Develop an Effective Material Flow Plan
Getting material flow right starts with understanding what’s already happening on the floor. That means inspecting how things move now, not just how they’re supposed to move on paper.
Step 1: Evaluate Your Current Workflow
Begin by walking through the entire process from the arrival of raw material to the exit of the finished product. Map it out and track how long each step takes and where materials tend to get stuck, double-handled, or slowed down. Flow diagrams and timing studies are useful here but so is input from the people doing the work. Operators are often the first to notice when a workstation is awkwardly placed, a step is taking longer than it should, or something in the layout forces unnecessary movement.
Step 2: Map and Analyze Material Movement
Once you’ve gathered the data, use CAD tools or flow simulations to visualize how materials move through the facility. These models help compare the distance materials travel, the time spent at each stage, and how efficiently the entire system runs. Compare different layout options to reduce travel time and streamline transitions. The goal is a layout that supports steady, logical movement.
Step 3: Plan the Layout with Your Team
Identifying problems is only half the job. Solving them requires working with engineers, operators, and facility managers to design a system that cuts unnecessary steps and keeps clean and raw areas separated. Adjust workstations, add conveyors if needed, and plan for either batch or continuous flow.
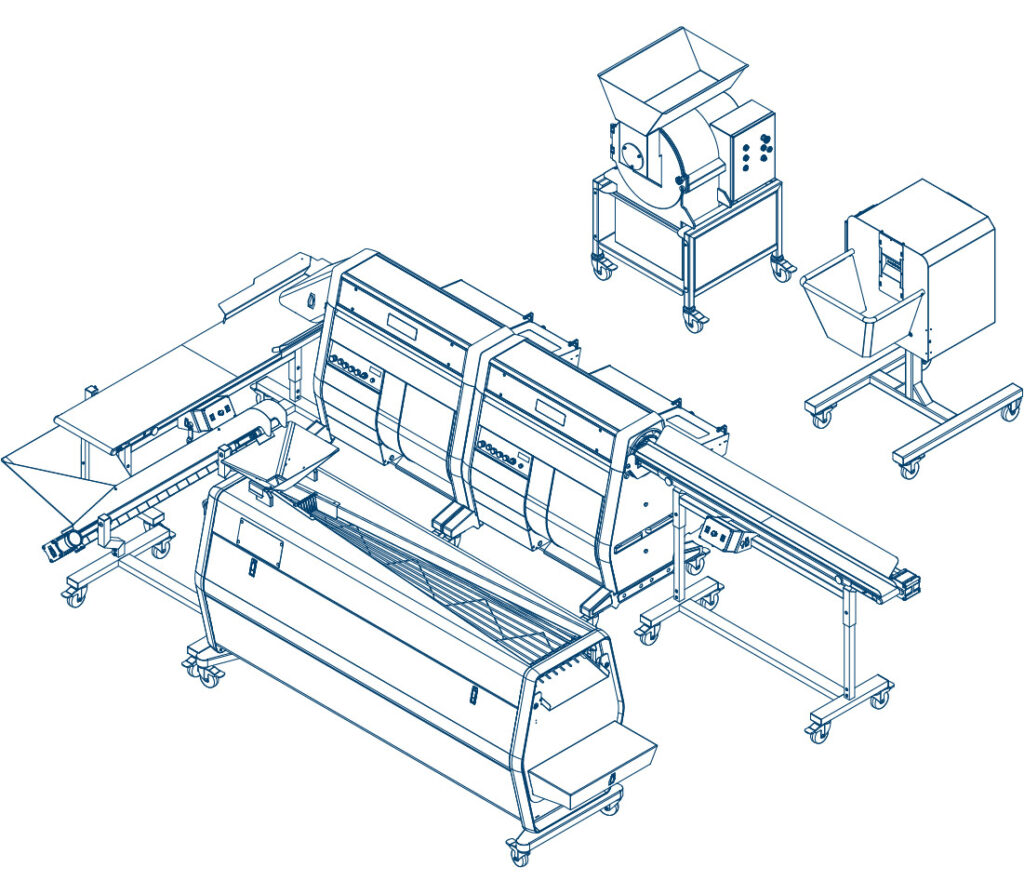
Step 4: Document the Flow in an SOP
Finally, capture the improved material flow in a clear, detailed standard operating procedure (SOP). A strong SOP outlines every state, including intake, processing, secondary steps, and waste disposal. It also ensures consistency from shift to shift and gives new employees a reliable guide to follow. In regulated industries like cannabis, SOPs are also key for compliance and help to meet documentation requirements around quality control, production planning, and batch traceability.
Material Flow Systems and Equipment
No material flow management plan is complete without the right equipment to support it. The type and configuration of this equipment will vary by facility size, product type, and budget, but some elements are universal.
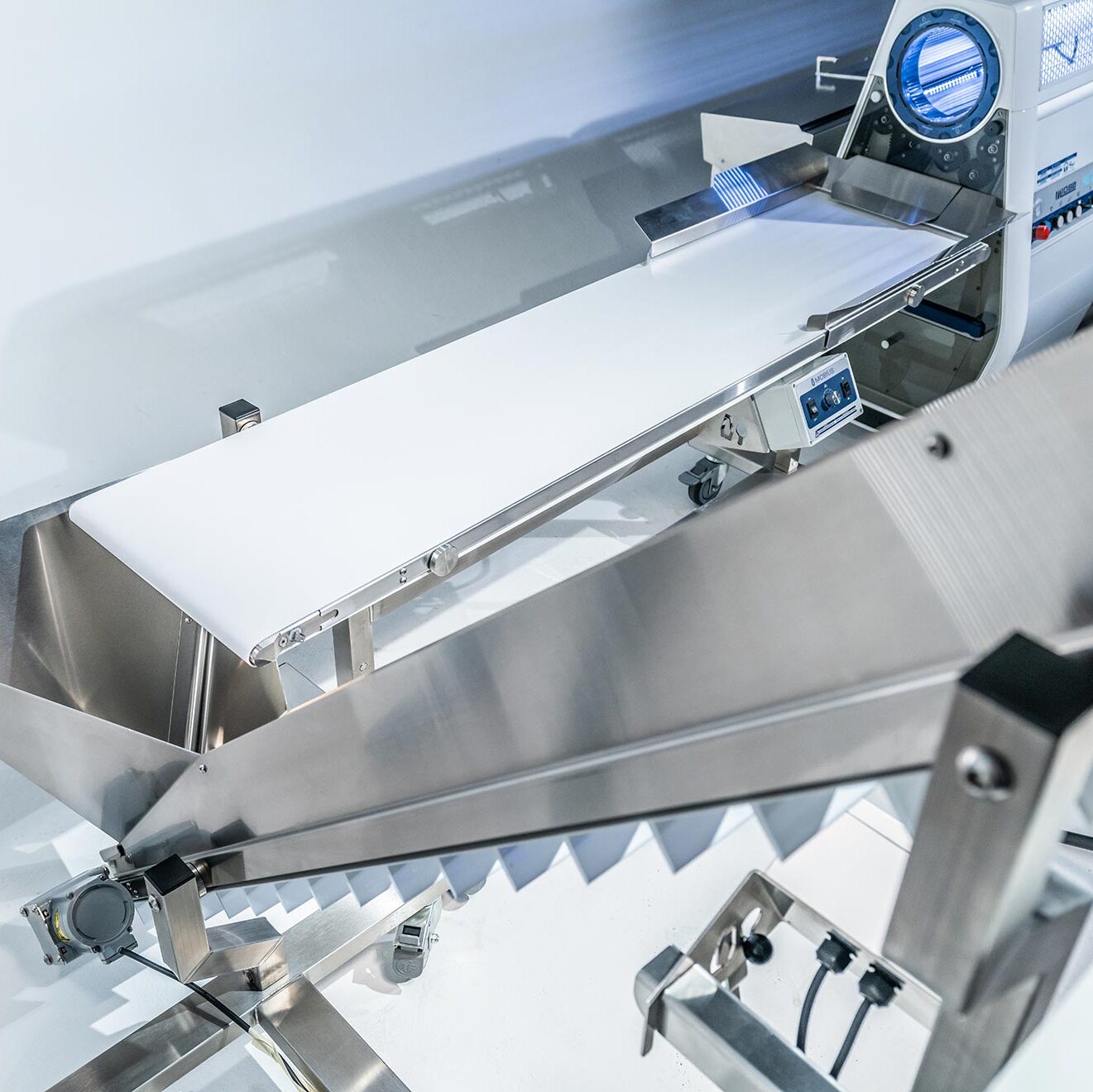
Conveyor systems are a cornerstone of efficient material flow. They reduce manual lifting, streamline transitions between stations, and can be configured to match both batch and continuous workflows. Mobius offers a range of automated conveyor systems designed for cannabis processing facilities, food production, and the supplement and cosmetic industries.
Other useful equipment includes:
- Automated sorters
- Weighing stations and labelers
- Real-time tracking systems
Strategic placement of equipment plays a large role in layout efficiency. Short, direct paths between related workstations and tasks are preferable for ergonomic flow. In multi-product facilities, modular systems or wheeled components offer flexibility when switching between product lines.
Challenges in Material Flow Optimization
Even the most carefully designed systems encounter challenges, especially in dynamic, multi-line facilities.
Common bottlenecks include congestion at weighing stations, trimming tables, or packaging zones. These issues often stem from poor timing, mismatched equipment speeds, or inadequate staging areas. Solutions may include increasing buffer zones, automating slow points, or refining SOPs to better coordinate staffing and materials.
Multi-product operations face additional hurdles. When one line is processing flower for infused edibles and another is preparing flower to be sold directly to consumers, material requirements, handling protocols, and sanitation needs can vary widely. In these cases, facilities benefit from flexible infrastructure, such as adaptable conveyors, removable partitions, and color-coded flow zones, to maintain efficiency and compliance.
Another challenge is balancing efficiency with quality control. As automation expands, it’s essential to match the speed and design of the equipment to the handling needs of the products being processed. For tasks that require visual checks, hand inspection, or delicate handling, operator involvement remains a key component. Material flow planning should account for this by including dedicated inspection zones, well-placed operator stations, and training protocols to make sure that quality remains high without sacrificing throughput.
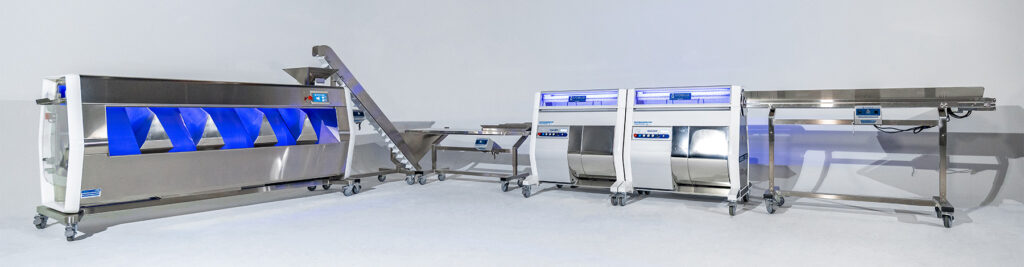
Optimizing Flow and Improving Results with Mobius
Whether you’re building a new facility or improving an existing one, material flow planning is one of the most valuable tools for enhancing productivity, consistency, and profitability. From cannabis and food production to specialty crops and health products, any facility that processes raw materials into finished goods stands to benefit from better flow design.
Mobius offers deep expertise in optimizing material flow systems for high-volume production. Explore our automated conveyors, facility design consultation services, and cannabis automation tools to streamline operations from input to output.
To learn more or speak with an equipment specialist, contact the Mobius team.