Material Preparation for Pre-rolls and Extractions: Cannabis Particle Size
In the cannabis industry, achieving the optimal particle size is critical for both pre-roll production and extraction processes. Producing the proper material grind size will maximize the quality of your products, as well as boost the processing efficiency of your extraction and pre-roll workflow.
Cultivators will often encounter downstream challenges with consistency, potency, and product quality when their starting material is not properly milled and processed. Commercial-scale cannabis cultivators seeking to streamline their processing operations must carefully consider how they mill their material. The quality and consistency of the final products are primarily determined by the input starting material and processing method chosen by the cultivators.
This guide explores the importance of particle size in cannabis and hemp material preparation, the types of milling methods, and how you can achieve the best quality through processing.
Importance of Particle Size in Cannabis Processing
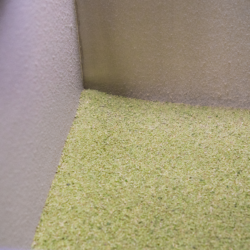
With cannabis and hemp being such delicate materials, precision in preparation leads to higher-quality products. Whether for pre-rolls or extraction, the correct particle size ensures consistent product quality, predictable cannabinoid levels, and better consumer satisfaction. As cannabis processing technologies advance, understanding and controlling particle size becomes crucial for any large-scale producer looking to maintain product quality.
Though the starting material may be the most potent or contain the best aromas and terpene profiles, if the flower does not get processed properly, the consumer experience with the final product can be negatively impacted. Even pre-rolls that contain the best flower may not produce the ideal smoke or burn consistently due to improper grind size and uneven filling. Extracts that were created using material that was poorly milled will not result in as highly potent concentrates.
The preservation of cannabinoids, as well as the potency of the final product is directly related to how the starting material was processed. Everything from preparation to storage will have an impact on the resulting product, which also influences the profit potential and ROI for that particular product.
Types of Cannabis Mills and Their Functionality
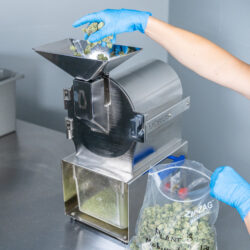
There are a few different methods producers may use to achieve the ideal grind size for their processing plans. Most cultivators will use a type of mill or industrial cannabis grinder to reduce the particle size of the cannabis material prior to extraction or pre-roll production to increase processing efficiency and product quality.
Various mills are available for cannabis processing, each offering unique benefits depending on the desired particle size, product type, and processing goals. The most commonly used mills include mechanisms that are either squeezing, breaking, or cutting up the material.
Hammer Mills
Hammer mills work by using a rotating shaft with attached ‘hammers’ to break down cannabis material through impact. The rotating mechanism breaks up the buds into smaller pieces and various screens may be included to allow the cultivator to achieve a specific grind size.
These mills can be versatile, making them suitable for initial size reduction and rough grinding. There is potential for heat generation with this method, so producers should be cautious about how this processing may impact their material’s quality. Additionally, due to the milling method, there is a chance the cannabis could be releasing chlorophyll and other undesirable compounds as it is being broken up by the impact of the hammers. For cultivators looking for speed and efficiency, hammer mills offer a balance, but they are best suited for rough milling rather than final preparation.
Blade Mills
Blade mills use sharp, rotating blades to cut the cannabis material into smaller pieces. The rotating blade speed can typically be controlled by the cultivator to achieve the best results based on the moisture content of the input material.
Blade mills are useful for processes that require a finer grind, though the uniformity of the output particle size may be harder to maintain consistently, due to the cutting mechanism and inability to control the specific grind size of the flower.
Burr Grinders
Burr grinders utilize two abrasive surfaces to grind material to a particular size. The distance between the burrs may be adjusted to control the output grind size. Burr grinders are particularly beneficial for preserving cannabinoids and terpenes, as they generate less heat during grinding. This method typically produces a consistent grind, though most are on a smaller scale and not suitable for commercial productions or large-scale operations.
Perforated Screen Mills
This type of mill uses a rotating component with perforated screens to gently push the cannabis material through the holes in the screen. Mills that utilize a perforated screen mechanism deliver ultra-consistent results because all of the flower is being milled to the same particle size. This style of mill often comes with various screen options, so the cultivator can swap out the screen with holes that match the intended particle size. Because there is little to no heat generated during this process, these mills are ideal for applications where maintaining the potency and aromatic profile of the plant is crucial, such as solvent-based and solventless extraction processes.
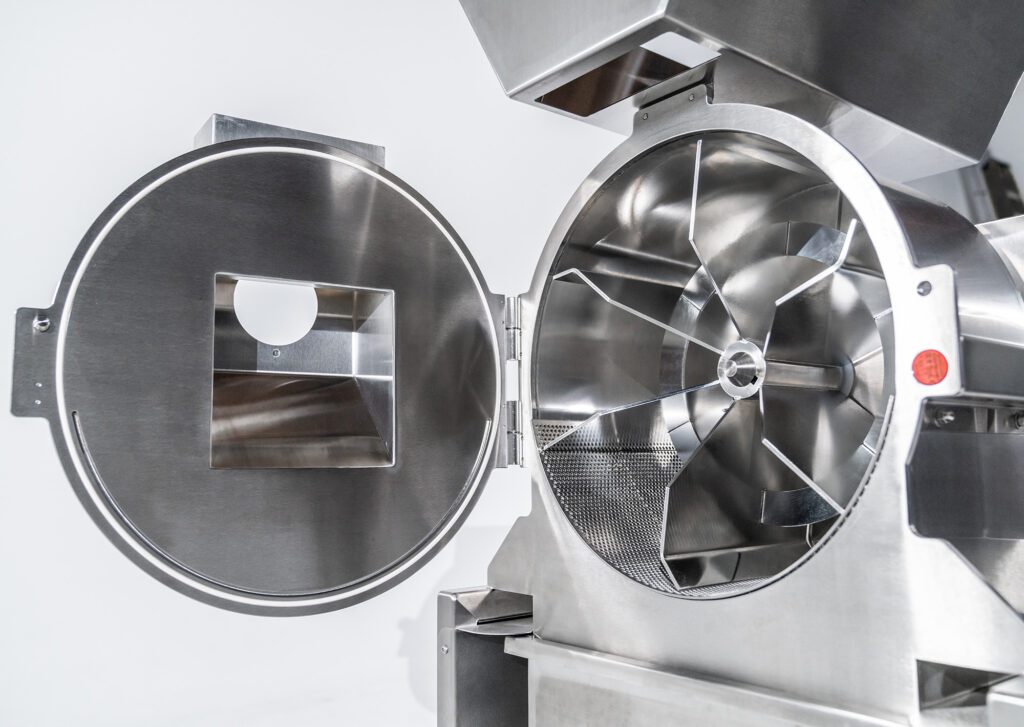
This type of mill uses a rotating component with perforated screens to gently push the cannabis material through the holes in the screen. Mills that utilize a perforated screen mechanism deliver ultra-consistent results because all of the flower is being milled to the same particle size. This style of mill often comes with various screen options, so the cultivator can swap out the screen with holes that match the intended particle size. Because there is little to no heat generated during this process, these mills are ideal for applications where maintaining the potency and aromatic profile of the plant is crucial, such as solvent-based and solventless extraction processes.
Choosing the Best Cannabis Mill
Throughout each stage of processing, cultivators want to ensure their products are maintaining their levels of cannabinoids and terpenes, and milling cannabis is no different. While the particle size is being reduced, you’ll want to keep the same purity and potency as when the bud structure was fully intact.
Though some processors may have concerns about how milling impacts cannabinoid recovery, studies have shown that with the proper milling techniques and conditions, the quality of the flower is not degraded, and the potency is not affected during the grinding process. In addition to the preservation of cannabinoids, the smaller particle sizes allow for improved extraction selectivity and higher recoveries of cannabinoids and terpenes.
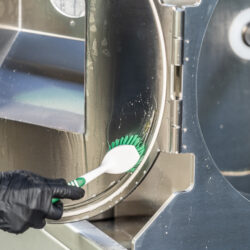
The type of mill or industrial cannabis grinder you choose will determine how your material’s particle size gets reduced. Processors will notice a difference between material that has been milled with a bladed mill that shreds the flower versus a perforated screen-style mill as it relates to the smokability of the product.
Factors to consider regarding the type of cannabis mill you choose include the mill capacity and size, the grinding mechanism, the material makeup and construction of the machine, the processing efficiency and throughput performance, the features of the mill (variety of options for particle size output, serviceability, cleanability, etc.), and the machine’s adherence to regulations and laws surrounding cannabis equipment, like GMP.
Challenges with Cannabis Material Preparation
Achieving consistent cannabis material preparation can be a challenge for processors when there are so many variables to consider. The type of flower, the cultivar, moisture content, bud density, and structure are all factors that will affect how the material responds to milling and particle size reduction. Processing efficiency and speed to market are also impacted by the milling method. Some of the main challenges with milling for pre-rolls and extraction include inconsistent cannabinoid delivery, poor extraction efficiency, and variable product quality.
Inconsistent Cannabinoid Delivery
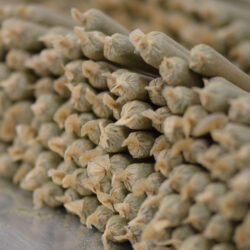
Achieving consistent cannabinoid delivery across different batches and harvests is one of the greatest challenges faced by cannabis processors. For joints and pre-roll production, the particle size of the material directly impacts the joint architecture and smokability of the product. A larger particle size typically results in longer-lasting effects but may deliver cannabinoids less effectively per puff. On the other hand, smaller particle sizes can deliver more cannabinoids quickly, but may not sustain the effects over longer periods of time.
Variations in particle size can also lead to “hot spots” in pre-rolls, where certain areas contain higher concentrations of cannabinoids, resulting in inconsistent potency. When particle size is inconsistent, the final product’s potency can fluctuate, impacting both consumer satisfaction and product reliability. Uniformity is essential, especially in pre-rolls, where uneven particle size distribution can lead to uneven burning and hot spots, affecting the smoking experience.
Extraction Efficiency
The particle size also directly affects extraction efficiency. For solvent-based extraction methods such as ethanol, hydrocarbon, or CO2, a smaller particle size increases the surface area for the solvent to reach all of the material, which can maximize yields. However, too fine of a grind can cause channeling, where the solvent bypasses some of the cannabis material and some areas are missed during the extraction process.
Over-grinding may also reduce cannabinoid preservation and extraction efficiency. Though, too coarse of a grind where the particle sizes have not been reduced enough, can result in incomplete extraction, which leaves valuable material behind and compromises the profit potential.
In solventless processes like rosin pressing, grind size influences how evenly pressure is applied, impacting both yield and product quality. When performing extraction at scale, the wrong grind size can lead to inefficiencies.
Product Quality and Consistency
If the cannabis material has too much variation in particle sizes, the resulting products will have varied quality. Using inconsistently milled material for production also affects the reproducibility of your extracts and pre-rolls, making it difficult to maintain a stable product line and create consistent products across the board. A large variation in particle sizes can lead to differences in texture, potency, and flavor, all of which impact the consumer experience.
The goal of milling is to create a homogeneous starting material and a consistent, specific particle size. Having consistently milled material also eliminates bottlenecks and downtime in processing that is caused by source material delays. Additionally, ensure your material maintains its potency throughout processing with a milling method that minimizes the losses of cannabinoids and terpenes from heat degradation.
Determining and Obtaining Optimal Cannabis Particle Size
For both pre-roll production and extraction, a uniform particle size ensures smoother production processes. Achieving the optimal particle size also has economic implications. Proper milling not only reduces processing times but also increases equipment uptime and reduces waste. For large-scale cannabis cultivators, these efficiency gains directly impact profitability.
Once you have determined what products you will be making and the best machine and milling methods for your needs, you’ll want to understand which particle sizes will provide the optimal processing efficiency and quality for your products. With complete control over the material output size, cultivators see bigger and quicker returns on their investment, delivering consistent products on a regular schedule.
Pre-Roll and Joint Production

Milling cannabis material for extraction procedures versus milling for pre-rolls requires different grinding styles and particle sizes. For pre-rolls, particle size is a critical factor in both product consistency and consumer experience. Cultivators can improve marketability and profit potential by creating custom blends of different particle sizes that satisfy the specific requests of their purchasers and meet current market trends. Studies have shown that a particular mix of certain particle sizes is proven to deliver the best joint architecture and smoking experience, improving overall smokability, reproducibility, and cannabinoid delivery.
Not only is the consumer experience improved with proper milling for pre-rolls, but with a better understanding of cannabinoid delivery and joint architecture, pre-roll manufacturers can provide more accurate reporting on their potency levels within the products. Additionally, consumers can be better informed regarding the products they’re using and the amounts of each cannabinoid being inhaled while smoking.
Milling for Pre-Rolls: Particle Sizes to Maximize Quality and Yield
A recommended particle size for pre-roll production falls around one millimeter, which is ideal for quick and efficient cannabinoid delivery. This particle size allows for more cannabinoids to be released and inhaled per puff, delivering the optimal smoking experience.
However, for a longer-lasting experience, a more coarse grind of three- to five-millimeter particle sizes can be ideal depending on the desired burn rate. These joints will burn slower and deliver the cannabinoids over a more extended period of time. Pre-roll manufacturers may also experiment with creating custom blends of particle sizes for a well-constructed joint that has consistent cannabinoid delivery and burns more evenly. A uniform grind ensures easy cone filling and rolling, a smooth draw, and consistent combustion.
Extraction Processing
With extraction processing, your milling technique and grind size will be determined by the type of extraction your facility is performing, whether that is solvent-based or solventless extraction. Additionally, your type of starting material (cannabis or hemp) will dictate the resulting products created. For hemp processing, the end goal is typically isolate, with producers trying to achieve as close to 100% purity as possible. With cannabis processing for extraction, the end goal is to create more connoisseur products like diamonds, shatter, live rosin, and crumble.
Effective particle size reduction before extraction ensures potency preservation while reducing the presence of any undesirable residues in your final product, such as chlorophyll and plant waxes.
Milling for Extraction: Particle Sizes to Maximize Quality and Yield
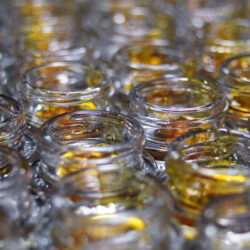
Ultimately, the grind size for both solvent-based and solventless extraction methods will depend on the preferences and processing choices of the individual producer. Extraction methods that use solvents are more easily distinguished when it comes to the optimal particle size for processing, while solventless extraction requires a more thought-out approach, taking yield and quality into higher consideration.
SOLVENT-BASED EXTRACTION PROCESSING
For solvent-based extractions, particle size plays a crucial role in optimizing the rate of extraction and the solvent’s efficiency. Finer particles expose more surface area, allowing solvents such as ethanol, CO2, or hydrocarbons to extract cannabinoids more effectively. However, the particle size must be balanced to avoid issues such as solvent channeling or excessive heat exposure, which can degrade cannabinoids. The right grind also ensures proper column packing, maintaining consistent pressure and flow rates.



PARTICLE SIZE | PRE-ROLLS | CO2 EXTRACTION | ETHANOL EXTRACTION | HYDROCARBON EXTRACTION | FRESH FROZEN |
1.6mm
1/16″ |
![]() |
![]() |
![]() |
![]() |
![]() |
2.0mm
5/64″ |
![]() |
![]() |
![]() |
![]() |
![]() |
3.2mm
1/8″ |
![]() |
![]() |
![]() |
![]() |
![]() |
4.7mm
3/16″ |
![]() |
![]() |
![]() |
![]() |
![]() |
6.4mm
1/4″ |
![]() |
![]() |
![]() |
![]() |
![]() |
12.7mm
1/2″ |
![]() |
![]() |
![]() |
![]() |
![]() |
19mm
3/4″ |
![]() |
![]() |
![]() |
![]() |
![]() |
- CO2: This solvent will require the finest grind out of all the solvent-based extraction methods. Aim to achieve between a one- and two-millimeter particle size, staying on the lower end of the range.
- Hydrocarbon: Slightly more coarse particles are best for this solvent. Cannabis material around two- to three-millimeters will prevent channeling in your process and allow the solvent to interact more thoroughly with the material.
- Ethanol: This is considered a more abrasive solvent, so the optimal particle size should be coarse, but not too large. In addition, proper column packing with uniformly milled material will ensure that the solvent flows evenly throughout the material and will prevent channeling during the process. This will maximize your extraction efficiency and deliver the best results.
SOLVENTLESS EXTRACTION PROCESSING
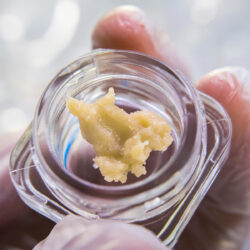
Rosin pressing requires precision in particle size reduction to balance yield and quality. Coarser particles may result in less efficient pressing, while over-ground material can clog filters and reduce the quality of the final product. Uniform particle size also contributes to better pressure distribution when pressing rosin, ensuring higher yields and better cannabinoid retention.
A finer grind will increase the surface area for pressing which enhances cannabinoid release, but a particle size too fine will release unwanted compounds into the extract. A grind of around two- to three-millimeters is often preferred by extractors to achieve the best balance between quality and yield.
A pre-press mold can be used to create uniform pucks, which prepare the material to be pressed evenly in micron filter bags. This preparation work prior to pressing will further enhance consistency and quality in rosin production by preventing blow-outs and hot spots.
Maintaining Potency Through Cannabis Processing
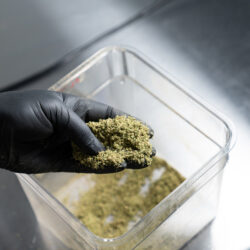
Maintaining cannabinoid potency is a major consideration throughout the milling process. Regardless of the product intent or particle grind size, your milling machine should be precise and deliver consistent results while preserving potency.
Mills like the Mobius M210 and M60 maintain an ultra-low speed during processing using a low-impact motor that protects the integrity of the trichomes. This type of mill minimizes any losses that may occur due to heat degradation. As compared to high-speed milling methods, the Mobius Mills produce little to no heat and friction, so the flower retains more terpenes and potency for higher-quality results. By using precise milling techniques, cultivators can balance efficiency with quality, ensuring that cannabinoid content is preserved throughout the processing stages.
In using a careful approach to milling and processing, producers can ensure that their products are meeting regulatory and consumer standards, as well as current market demands to achieve maximum returns. With optimized particle size reduction, cultivators can overcome most of the challenges associated with cannabis material preparation, allowing for improved outcomes.
Optimized Cannabis Milling for Better Products
In the cannabis industry, achieving optimal particle size is essential for both pre-roll production and extraction processes. Proper milling techniques ensure consistency in product quality, preserve cannabinoids, and streamline production processes. Implementing the right milling solution is not just about improving product quality—it’s about enhancing operational efficiency and profitability.
For cannabis cultivators looking to elevate their processing capabilities, investing in high-quality milling solutions is a step toward ensuring consistent, high-quality products that meet consumer demands and regulatory standards. Contact Mobius today to learn about how our milling machines can optimize your processing workflow.
Let’s Talk Today
Utilizing the right operating procedures, you can expect enhanced product quality. See how Mobius can help with your cannabis automation.