Optimal Processing Room Conditions: Achieving Ideal Cannabis Humidity and Temperature Levels
In the competitive cannabis industry, precision is crucial. For a cannabis grower to scale their operations effectively, maintain quality, and boost profits, they need comprehensive control over everything — including the temperature and humidity levels plants are exposed to throughout each stage of processing.

The temperature and humidity of your processing room play a pivotal role in determining the quality and longevity of your final product. For cultivators operating at scale, managing these environmental conditions preserves product integrity and customer satisfaction.
Precise temperature and humidity levels are a crucial component of quality control, and it’s the key to ensuring compliance, optimizing yield, and meeting the high expectations of discerning customers. Improper humidity levels can lead to mold, terpene degradation, and cannabinoid loss, while fluctuations in temperature can compromise potency and flavor profiles.
Here’s your expert guide to maintaining optimal humidity and temperature levels throughout the cannabis cultivation and processing journey.
What is Humidity, and Why Does It Matter in Cannabis Cultivation?
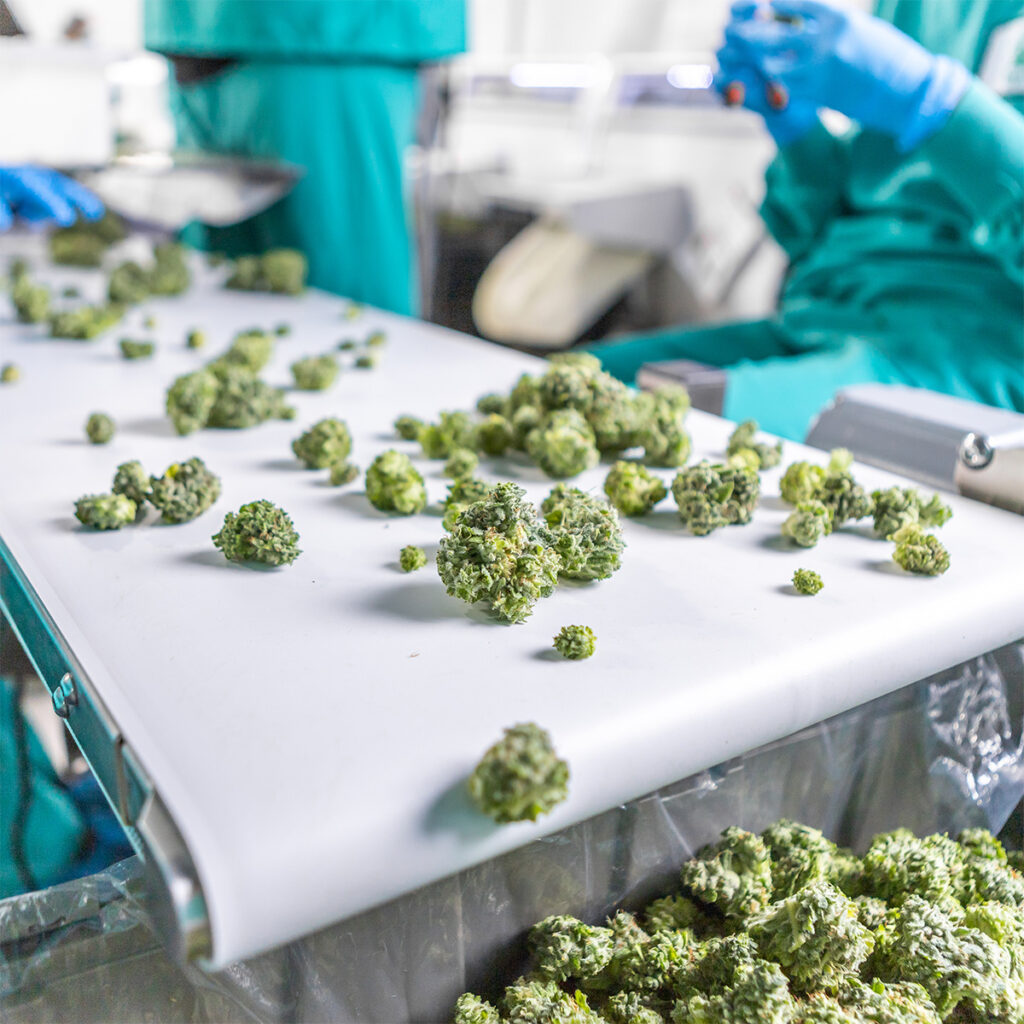
Humidity refers to the level of moisture present in the air and is typically measured as relative humidity (RH).
In commercial cannabis production rooms, RH is a crucial parameter for regulating the moisture content in cannabis during drying, curing, and storage. Relative humidity, expressed as a percentage, indicates the amount of water vapor in the air compared to the maximum amount the air can hold. This balance is essential in maintaining the ideal conditions for cannabis to retain its quality.
Maintaining proper humidity levels is critical throughout all stages of cannabis cultivation and processing, from growing to trimming, curing, and storage.
If the moisture level in an environment is too high, it can lead to mold and microbial growth, rendering products unsafe, or even unsellable. However, if humidity is too low, the plant material can dry out, and trichomes become brittle. Those trichomes can then degrade, diminishing the potency, flavor, and aroma of the product.
Maintaining a consistent humidity (between 55% and 65%, according to ASTM standards) is essential to mitigating these risks. Beyond affecting the quality and effectiveness of cannabis products, maintaining the ideal humidity level in your cannabis facility helps to ensure compliance.
Mold or microbial contamination due to high humidity can result in failed safety inspections and financial losses. Furthermore, overdried cannabis may fail to meet weight requirements, directly impacting revenue. Consistent RH not only ensures product safety and integrity but also helps cultivators meet stringent quality control standards required in commercial cannabis operations.
The Optimal Humidity Range for Cannabis Processing Rooms
In every stage of the cannabis processing journey, from harvesting and trimming to drying, curing, and storing, maintaining precise control over relative humidity is how cannabis cultivators can ensure they’re getting the most value out of their cannabis plants.
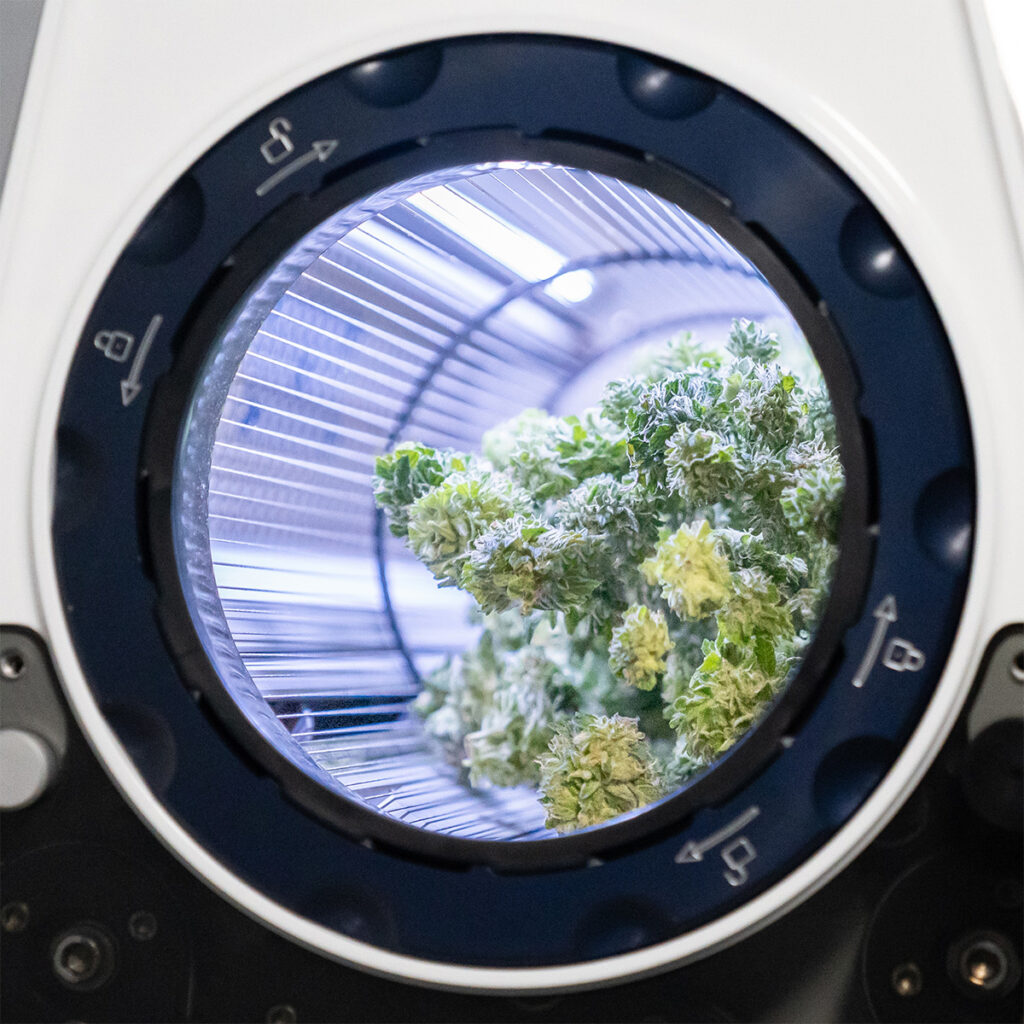
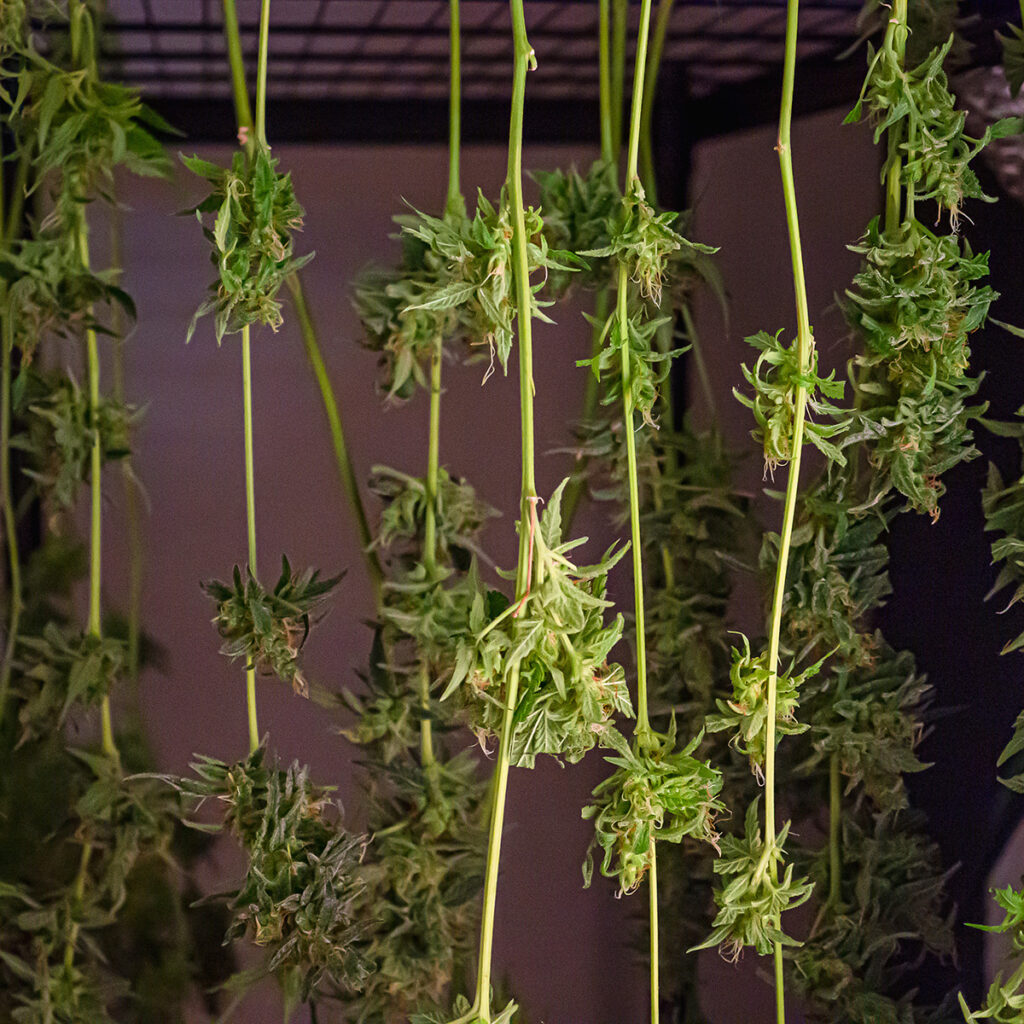
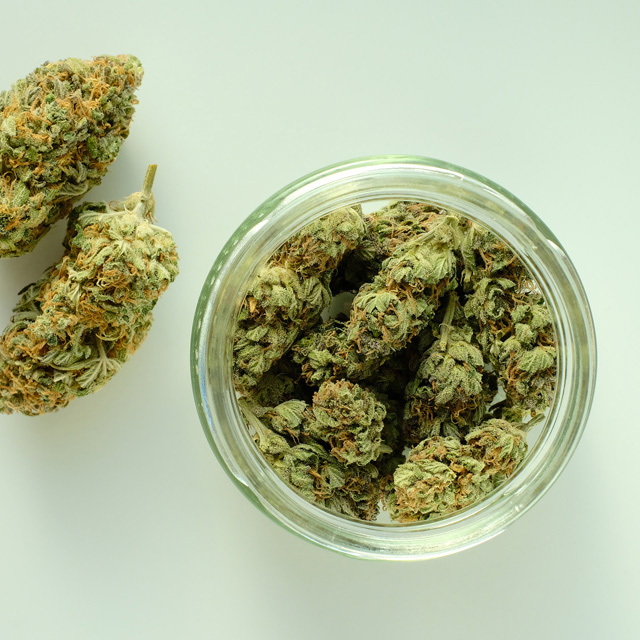
Although the ideal humidity and temperatures of processing rooms and spaces for drying, curing, and storage will often be relatively similar, there are differences between the best humidity levels to maintain at each stage of the cannabis processing experience. For instance:
- Trimming: During trimming, cannabis plants are handled extensively, and maintaining a relative humidity range of 55–60% is crucial. At this stage, the moisture in the plant should be controlled to avoid excessive dryness that can cause the trichomes to break off. Conversely, too much humidity can make the plant sticky and difficult to handle, slowing down the trimming process and compromising product consistency.
- Drying: It’s easy to assume humidity should be at a minimum during the drying process. However, during this stage, maintaining a humidity level of 55–60% allows moisture to leave the plant at a controlled rate. This prevents the outer layers from drying too quickly while leaving the interior overly moist — a condition that can lead to uneven curing and a higher risk of mold. Slow and controlled drying helps to preserve terpenes and potency, minimizing the degradation of cannabinoids.
- Curing: During curing, the RH range shifts to 50–60%. This level allows residual moisture within the buds to redistribute evenly, preventing brittleness and maintaining texture. Proper curing conditions enable terpenes to develop fully while preventing degradation, resulting in a more aromatic and potent product. At the same time, microbial growth is minimized, ensuring compliance with safety standards.
The Consequences of Poor Humidity Control
Limited control over humidity, temperature, and moisture levels in a processing environment creates a host of problems. If the RH falls below the recommended range at any stage, the cannabis plant becomes overly dry. Trichomes grow brittle and detach from the plant material, reducing potency as cannabinoids and terpenes are lost.
Additionally, low humidity accelerates terpene evaporation, which diminishes the aroma and flavor profile of the product, leaving it harsh and less appealing to consumers. For cultivators, this can translate to a direct loss of product value.
On the other hand, high humidity levels create the perfect environment for mold and microbial growth. This is especially dangerous during drying and curing, as moist buds can become breeding grounds for contamination. Not only does this pose a significant health risk to consumers, but it also leads to failed compliance testing and financial losses. Moldy products must be discarded, and the entire batch may require rework or additional processing to mitigate contamination.
The Ideal Temperature and Humidity Combinations for Cannabis
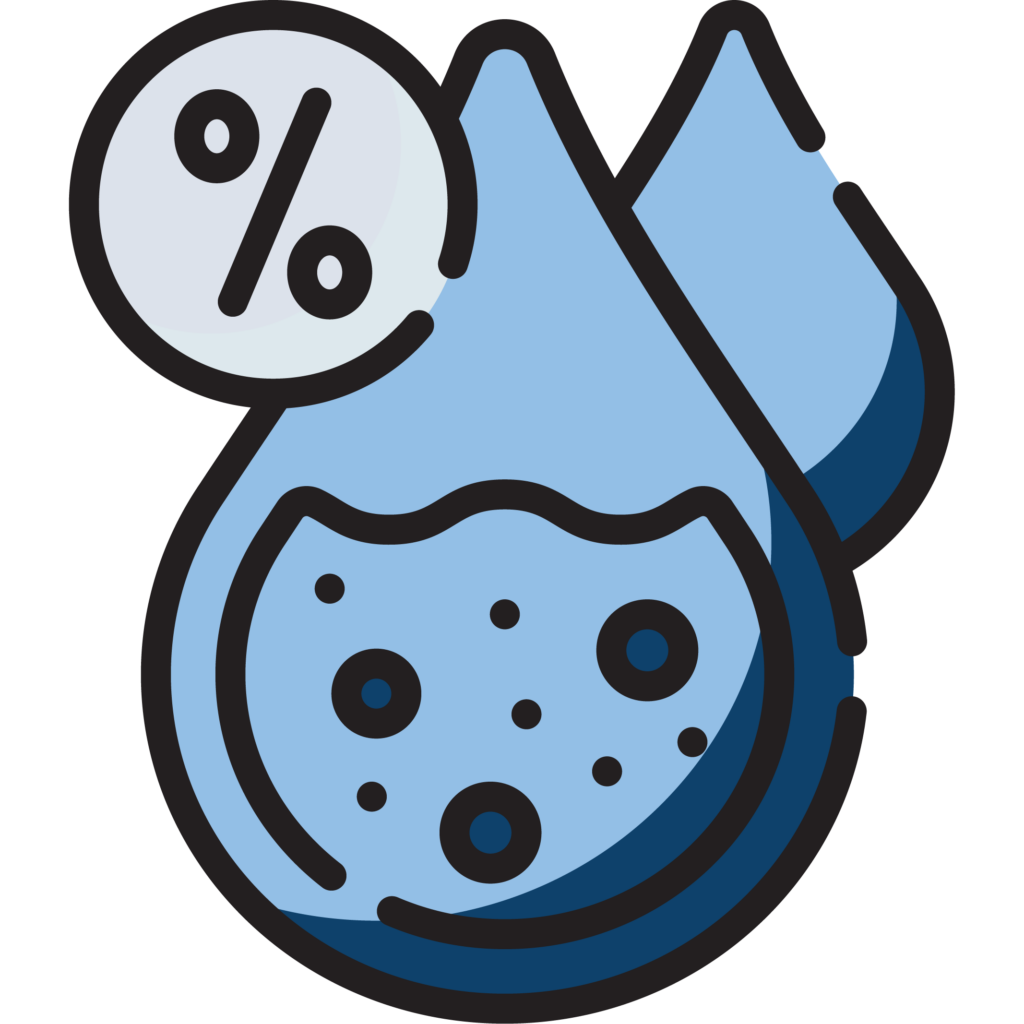
Temperature and humidity are interdependent variables that significantly align to influence the quality, safety, and consistency of cannabis products. In processing rooms, the interaction between these two factors determines how effectively cannabis is dried, cured, and stored.
Ultimately, finding the ideal temperature and humidity levels can be complex, as it may depend on the type of cannabis plant you’re cultivating. According to one review, a temperature of 65–70°F is ideal for drying flowers, combined with a 50–55% relative humidity. However, the internal moisture content of your cannabis buds and other factors can come into play.
Maintaining a Balanced Climate
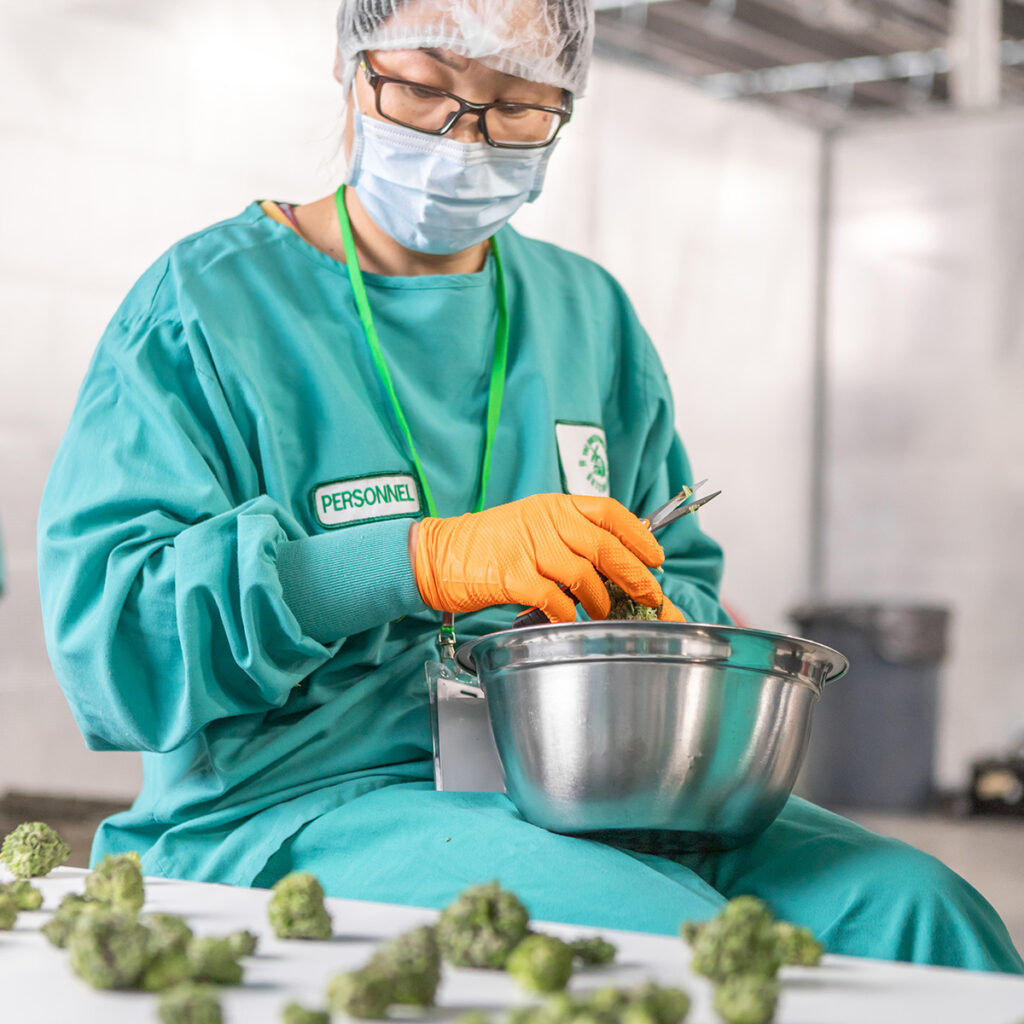
In a controlled processing environment, temperature affects how quickly moisture (water vapor) evaporates from plant material, while relative humidity (RH) regulates how much moisture the air can hold. For example, high temperatures with low humidity accelerate drying, which can cause trichomes to degrade and terpenes to evaporate. Conversely, high humidity with low temperatures slows drying excessively, increasing the risk of mold or microbial contamination.
Balancing temperature and humidity is not only crucial for product quality but also for worker safety. Excessive heat or high humidity can create uncomfortable or unsafe working conditions, affecting productivity and compliance with occupational health standards. Maintaining an ideal environment optimizes both product results and workplace efficiency.
For both safety and optimal product protection, here are some recommended ranges to consider:
- Trimming: 60–70°F (16–21°C): During trimming, maintaining a temperature range of 60–70°F helps stabilize the moisture content of the plant material while making it easier to handle. At this stage, RH should be kept at 55–60% to prevent the buds from becoming sticky or overly dry.
- Drying: 60–70°F (16–21°C): The ideal temperature for drying is between 60–70°F, complemented by an RH of 55–60%. These conditions allow for a slower drying process which prevents uneven results.
- Curing: 60–70°F (16–21°C): Curing requires a dark and climate-controlled environment, with ideal temperatures ranging from 60–70°F. At this stage, the RH should be around 50–60% to allow moisture to redistribute evenly within the buds. These conditions enable the full development of terpenes and cannabinoids while preventing brittleness and terpene loss.
Process | Temperature Range (°F) | Temperature Range (°C) | Humidity Range (%) |
---|---|---|---|
Trimming | 60–70°F | 16–21°C | 55–60% |
Drying | 60–70°F | 16–21°C | 55–60% |
Curing | 60–70°F | 16–21°C | 50–60% |
How to Monitor and Maintain Optimal Processing Room Conditions
Achieving and maintaining the right temperature and humidity in cannabis processing rooms is essential to creating high-quality products and adhering to industry standards. The right strategy will usually depend on a multi-faceted approach to using the right technologies and best practices.
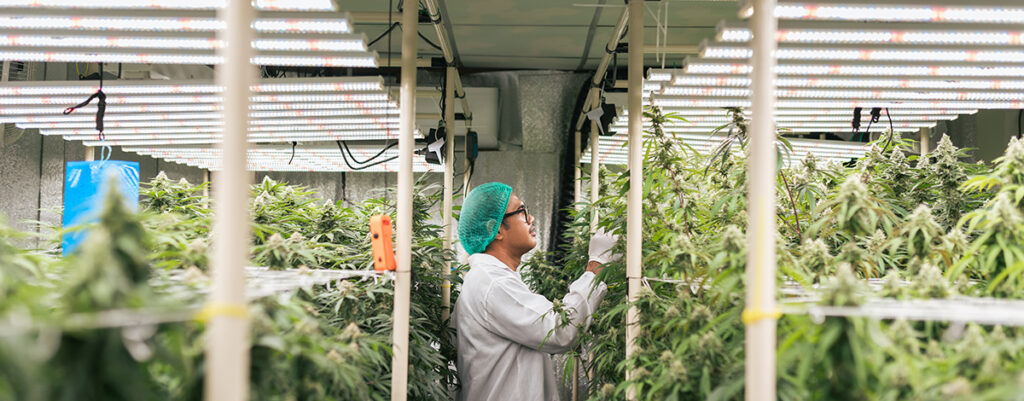
Tools and Technologies for Temperature and Humidity Control
Advancements in technology have made monitoring processing room conditions more efficient and precise. Some of the most effective tools include:
- IoT Sensors: Internet-connected sensors continuously track temperature and relative humidity (RH) levels, providing real-time data. These sensors often integrate with centralized monitoring systems, allowing cultivators to view environmental metrics remotely.
- Automated Climate Control Systems: These systems use sensors to adjust HVAC systems, humidifiers, and dehumidifiers automatically, maintaining the desired conditions without manual intervention.
- Data Loggers: These devices record environmental conditions over time, helping cultivators identify patterns or inconsistencies that could impact product quality.
- Alert Systems: Many monitoring tools come equipped with alert features that notify users via text or email if temperature or humidity falls outside the acceptable range.
Processes for Adjusting and Maintaining Room Conditions
Various technologies can also help cannabis growing experts and cultivators maintain the right humidity and temperature levels in various environments. For instance:
- HVAC Systems: High-quality HVAC systems regulate airflow and temperature in processing rooms. These systems are essential for maintaining a stable environment, especially in large-scale facilities with multiple processing areas.
- Dehumidifiers and Humidifiers: Dehumidifiers remove excess moisture from the air, while humidifiers add moisture when the environment becomes too dry. Both are critical for fine-tuning RH levels to meet the needs of each processing stage.
- Insulation and Sealing: Proper insulation and sealing prevent external factors, such as weather or adjacent rooms, from influencing the processing room environment.
When using these systems, make sure you implement constant and routine maintenance checks to ensure continued efficacy.
The Value of Consistency
The key to success is consistency across all processing stages, from trimming and drying to curing, packaging, and storage. Variations in conditions can cause unwanted changes in moisture levels, leading to terpene loss, brittleness, or microbial growth. For example, transferring cannabis from a dry curing room to a humid packaging area can reintroduce moisture, risking mold development.
Creating a unified climate control strategy for all rooms minimizes these risks. Automated systems can standardize conditions across multiple spaces, ensuring a seamless transition between stages.
Setting the Standard for Cannabis Processing
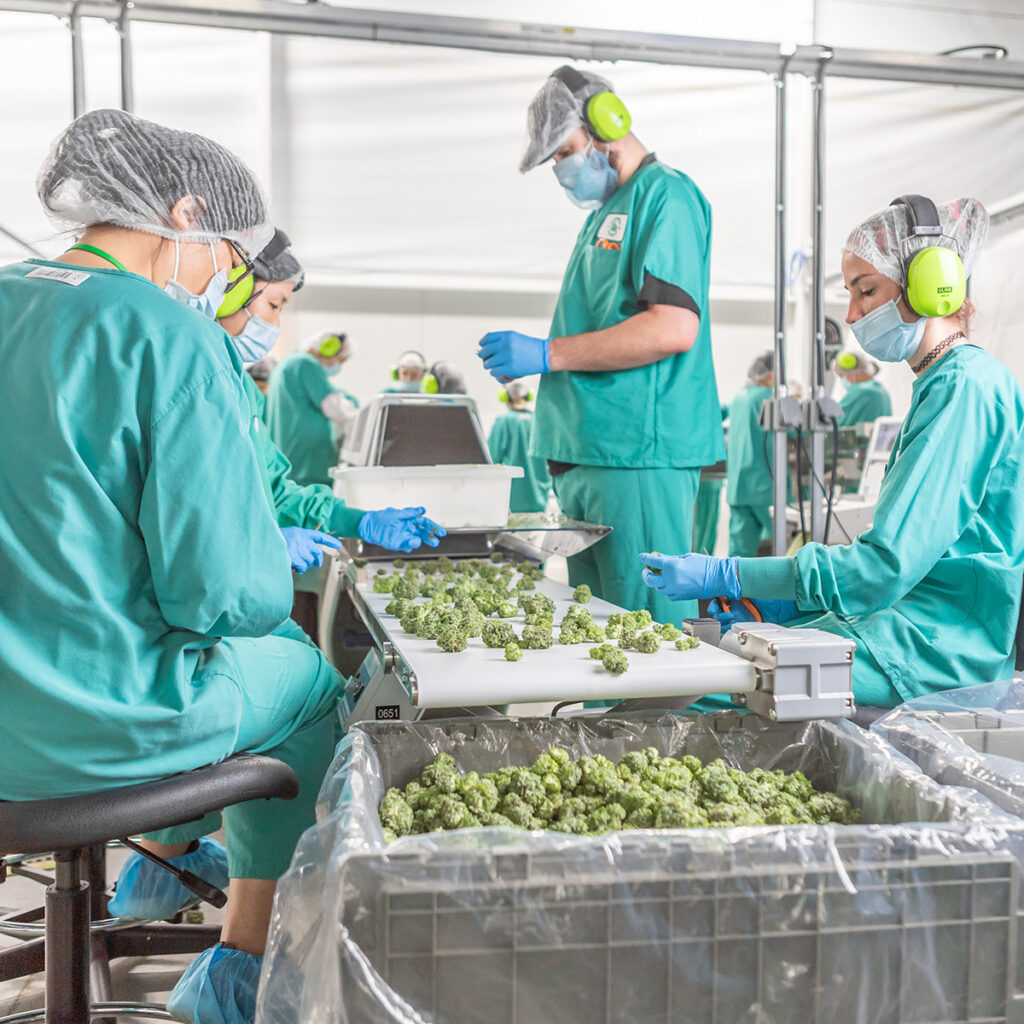
Maintaining the ideal temperature and humidity in cannabis processing rooms is not just a best practice, like following the right cleaning and maintenance strategy. It’s critical to ensuring product quality, safety, and profitability. Creating the perfect environment for cannabis processing is how you preserve potency, aroma, and overall product quality while minimizing the risks of product degradation, mold growth, and damage.
Balancing temperature and humidity ensures you can consistently deliver a superior product that meets consumer expectations and adheres to strict regulatory requirements. Mobius offers unparalleled expertise in post-harvesting and automation solutions to help you maintain optimal processing conditions. Whether you need to refine your facility’s climate control or streamline your processing workflow, our experts are here to guide you. Ready to take your cannabis processing to the next level? Speak with our post-harvesting and automation experts about how you can optimize your processing room conditions. Contact us today.
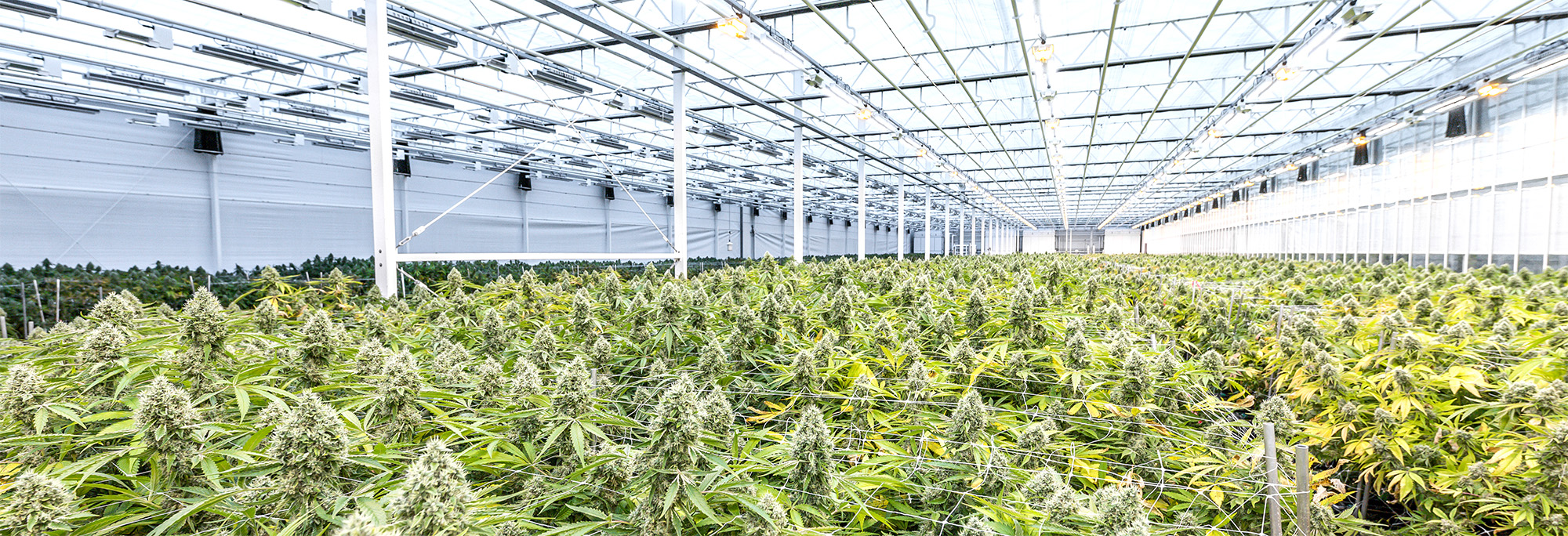