Conveyor Belt Maintenance: A Complete Guide
In any high-production facility, conveyor belts do more than move products — they set the pace for your entire operation. If the belt stops, so does everything else, making conveyor belt maintenance one of your most important tasks.
Mobius conveyors are trusted by commercial-scale cultivators who can’t afford downtime or product contamination, and this article reflects what we’ve learned through years of supporting post-harvest facilities and other GMP-sensitive operations.
Whether you’re handling cannabis, supplements, or food products, the principles of proper maintenance are the same. Here we’ll cover the best practices for maintaining your conveyor belt system, from preventive maintenance and cleaning to inspection checklists.
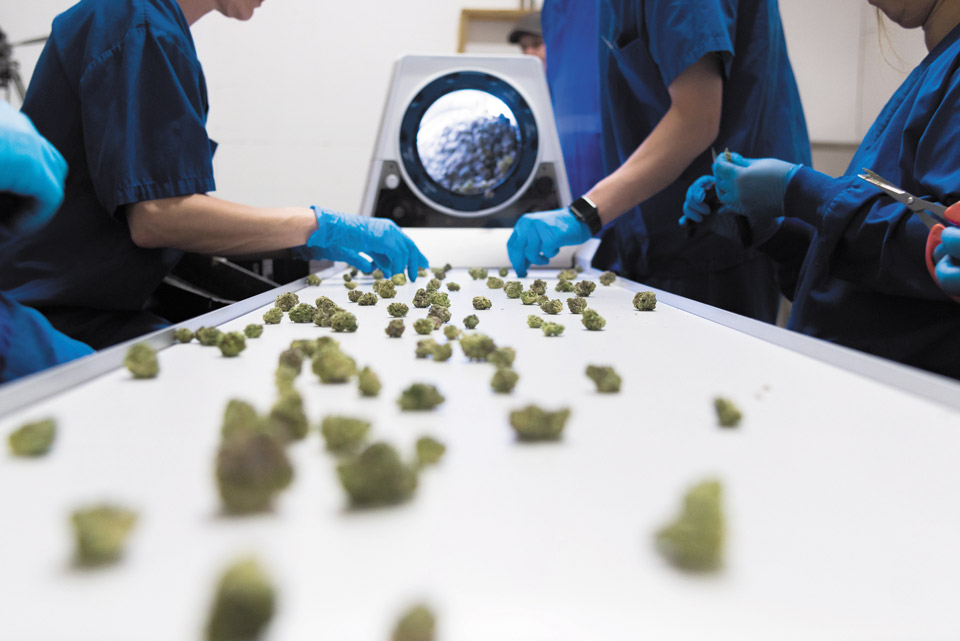
Why Conveyor Belt Maintenance Matters
In high-throughput production, reliability is everything. A conveyor belt system may seem straightforward, but it involves many moving parts working in precise coordination. A single issue, such as belt slippage, buildup, or misalignment, can trigger a maintenance scramble.
Routine, preventive maintenance helps avoid these problems, keeping the operation running smoothly and efficiently, and minimizing emergency repair costs.
In food-grade and agricultural processing environments, maintenance takes on an even more important role because of strict cleanliness and material handling standards. Routine care is often the only way to stay compliant.
Main Components of a Conveyor Belt System
Every conveyor setup is different, but the core components tend to include the following:
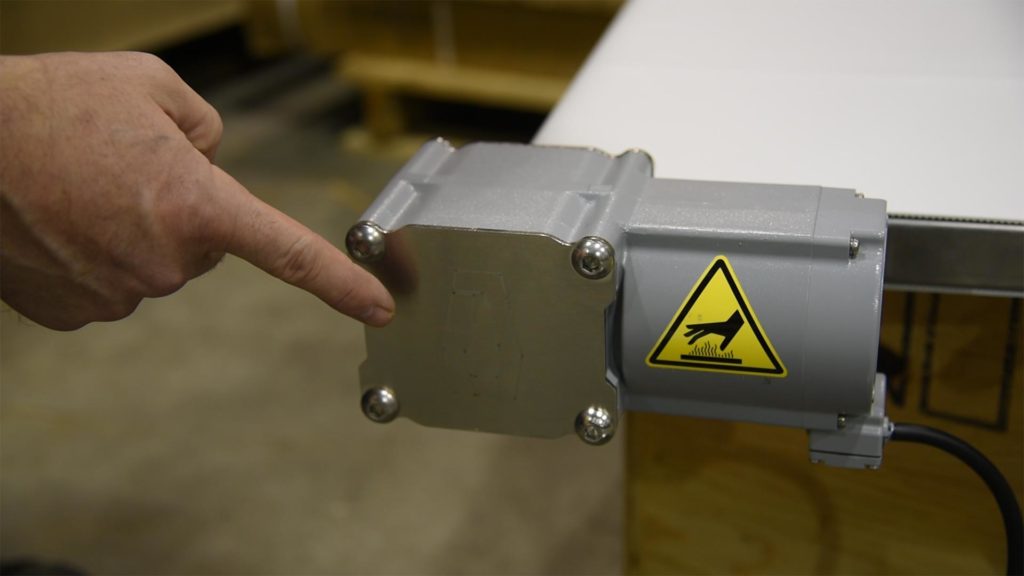
- The Belt: This is your primary contact surface. It can be made from a variety of materials, including food-safe plastics, rubber, or stainless mesh.
- Pulleys and Rollers: These support and drive the belt, keeping it taut and aligned.
- Motor and Drive Mechanism: This is what powers the system and includes the motor, gearbox, and controls. Motor alignment and performance will directly affect the load your system can handle and belt speed.
- Tracking and Tensioning System: This helps to keep everything in line. It ensures that the belt stays centered and maintains the proper tension.
Each of these components requires regular inspection and maintenance. Neglect any one of them and you might be subject to faster wear and tear, unplanned downtime, or unsafe working conditions.
Common Conveyor Belt Issues
Even in the best-designed systems, wear is going to happen. Fortunately, many problems can be caught or prevented with regular maintenance.
What to Watch For
The same issues frequently show up across most conveyor belt systems and include:
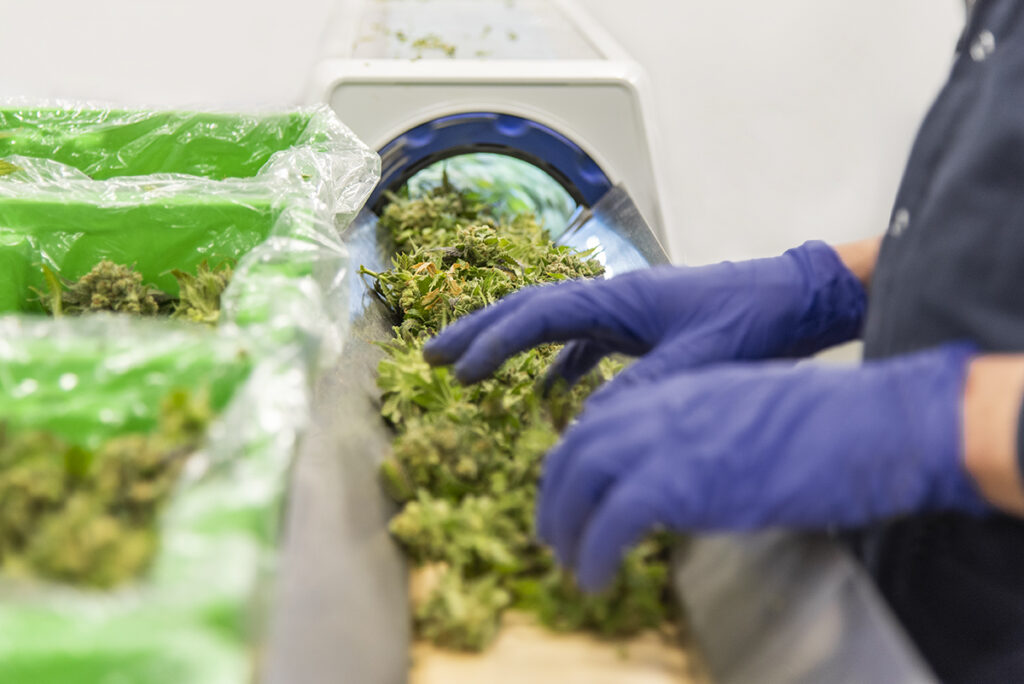
- Belt Misalignment – When belts drift off center, they can wear unevenly, have frayed edges, or cause jams.
- Belt Slippage – Caused by improper tension or a pulley problem. It shows up as inconsistent speeds or sudden stops.
- Material Buildup – Especially common in sticky, resinous, or dusty environments, product residue or debris can accumulate under the belt or around the rollers.
- Excessive Wear – Over time, belts may crack, stretch, or lose thickness, which increases the risk of rupturing mid-shift. This is especially a concern in high-friction zones.
- Improper Lubrication – Dry or over-lubricated components can cause friction, corrosion, or failure, leading to costly delays and repairs.
- Motor Issues – Vibration, unusual noises, or temperature spikes may mean the belt is misaligned or overloaded, or there’s a lubrication problem.
Preventive Maintenance Reduces Downtime
Daily inspections are the first line of defense in preventive maintenance. Catching the small problems early, like a loose bolt or a slight misalignment, can prevent larger failures and costly repairs.
The rest of the issues can be avoided with scheduled conveyor maintenance. A consistent schedule will include tasks such as cleaning the belt, adjusting tension, checking the tracking, and lubricating moving parts. Regularly performing these small tasks will reduce long-term repair costs and downtime.
Best Practices for Conveyor Belt Maintenance
You don’t need a large maintenance team to do this well. You just need a system, a standardized process, and people trained to follow it. A comprehensive maintenance plan will include regular inspections, targeted cleaning, staff training, and documentation.
Routine Inspections
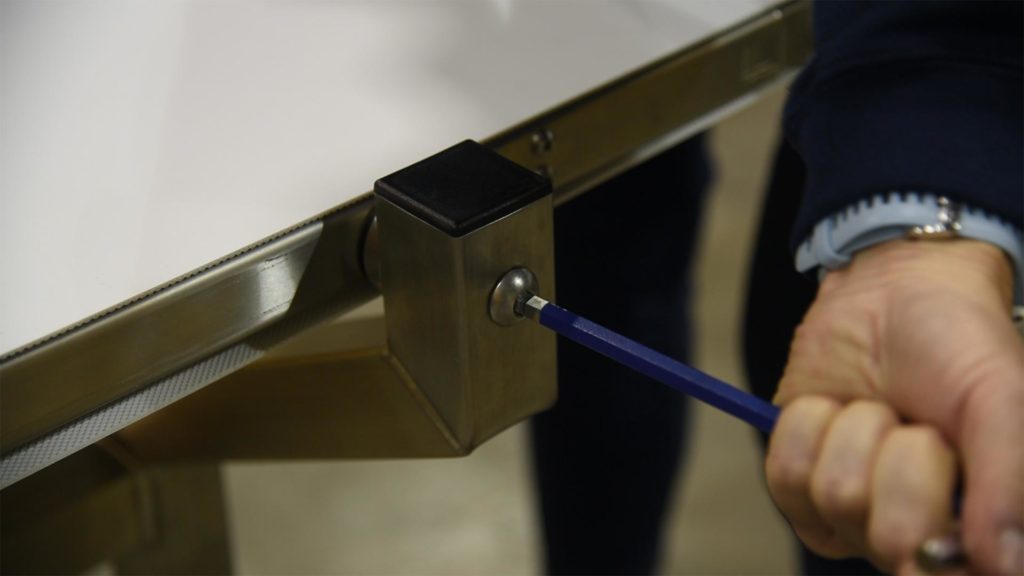
Regular conveyor inspections should include:
- Checking for frayed or cracked belts
- Monitoring belt tracking and tension
- Testing motor performance and noise levels
- Examining roller alignment and rotation
- Inspecting bearings for overheating or wear
Be sure to document everything. Logging your inspection results can help identify patterns or recurring issues. For example, a belt may always drift to one side, which could be a belt issue or a structural one. Documentation can help you see the difference.
Keeping track of issues can help determine if they are tied to specific production loads or environmental conditions. This can help you predict part replacements and adjust maintenance schedules.
Cleaning and Sanitizing
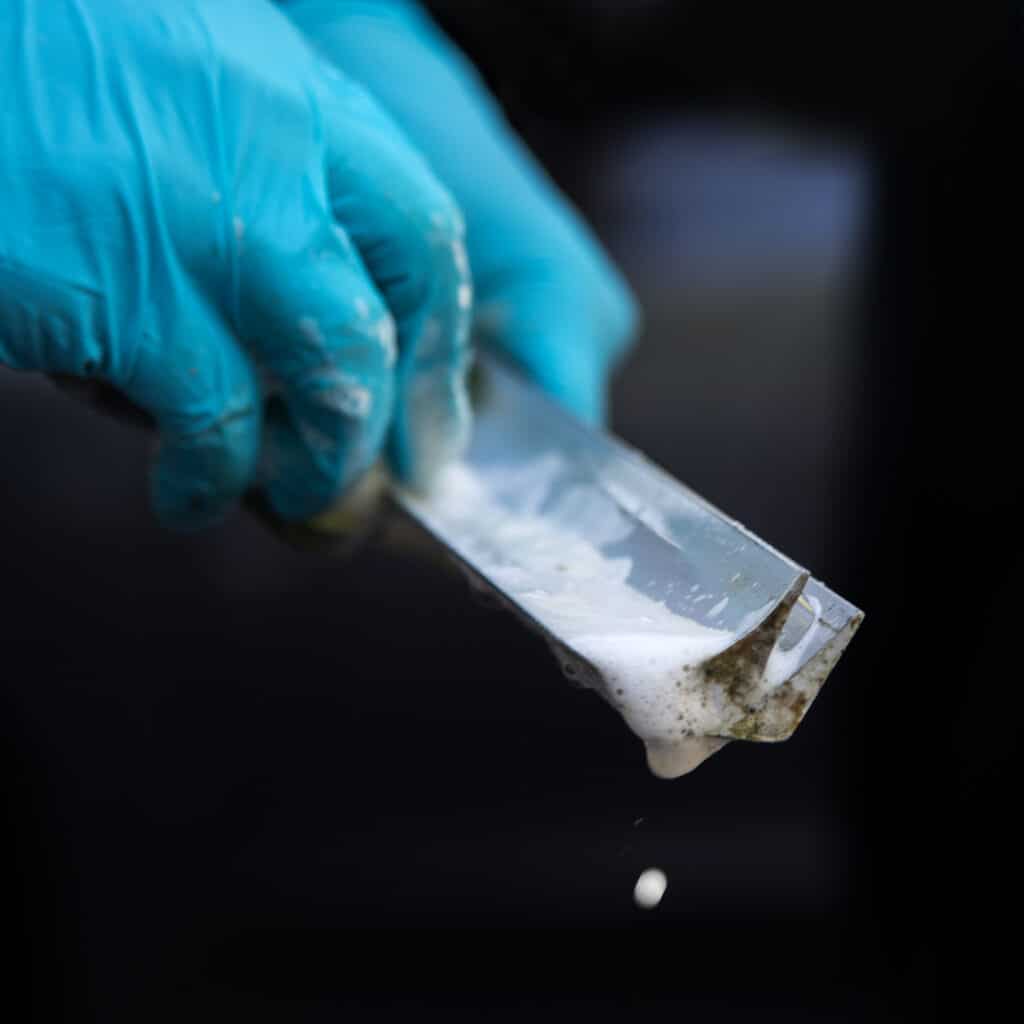
Industries like cannabis, supplements, and food production have strict requirements for cleanliness and sanitization. When product residue builds up, it creates friction, throws off alignment, and violates sanitization standards, which can impact regulations such as GMP compliance.
In these types of environments, conveyor belts must be cleaned daily using a non-corrosive and food-safe cleaner like Step 1 Cleaner and then sanitized to eliminate germs. Deep cleaning should be done on a regular schedule, especially if your products are sticky or powdery.
While pressure washing can be effective for cleaning conveyor systems, care must be taken to avoid direct exposure of motor systems and electrical components to water. After washing, it is critical to properly dry all components to prevent microbial growth or corrosion.
Staff Training
Most breakdowns start small — an unusual belt movement, a strange sound, a sudden shift in load speed. Your operators are in the best position to spot these issues, as long as they know the signs.
Train every shift to recognize the warning signs. Structured onboarding and refresher programs reinforce the correct routines for cleaning, reporting, and logging. You want to encourage a culture of ownership across teams to reduce preventable failures and extend equipment life.
Conveyor Belt Maintenance Checklist
If it’s not documented, it’s not repeatable. A standardized checklist ensures consistency, no matter who’s on shift. The checklist will vary depending on your usage of the conveyor, frequency, types of materials, and conveyor system, however this is a general guide for proper maintenance.
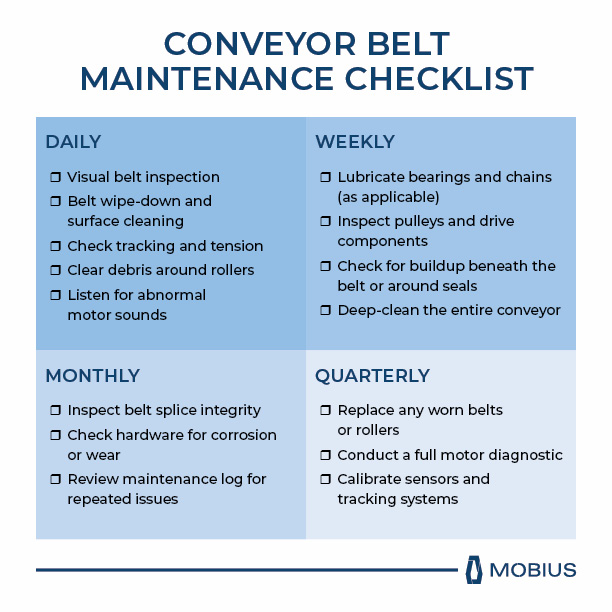
Daily Checklist
- Visual belt inspection
- Belt wipe-down and surface cleaning
- Check tracking and tension
- Clear debris around rollers
- Listen for abnormal motor sounds
Weekly Checklist
- Lubricate bearings and chains (as applicable)
- Inspect pulleys and drive components
- Check for buildup beneath the belt or around seals
- Deep-clean the entire conveyor
Monthly Checklist
- Inspect belt splice integrity
- Check hardware for corrosion or wear
- Review maintenance log for repeated issues
Quarterly or Annual Tasks
- Replace any worn belts or rollers
- Conduct a full motor diagnostic
- Calibrate sensors and tracking systems
For operations working toward GMP certification, this kind of schedule is essential and helps to make sure you’re meeting all the standards.
Choosing the Right Conveyor Belt for Your Industry
Choosing the right equipment for your setup can play a large role in long-term maintenance. Not all belts are created equal, and this is especially true when choosing equipment for specialized production.
Belt Material Matters
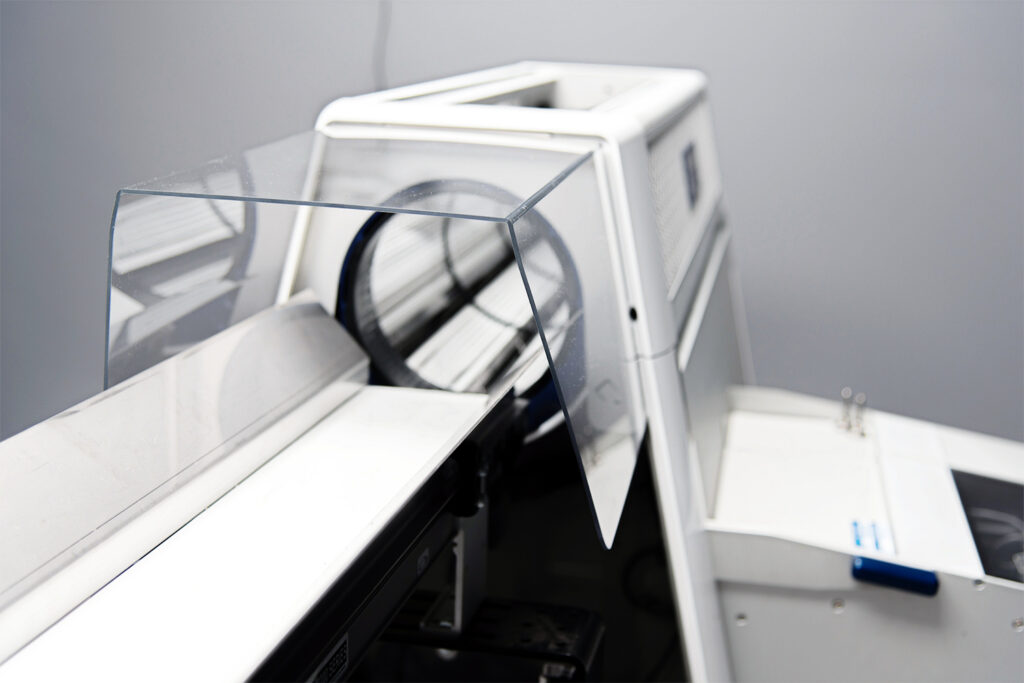
- Food-grade belts – Non-porous, easy to sanitize, and compliant with FDA regulations.
- Cold-resistant belts – Maintain flexibility and function at low temperatures. For example, Mobius conveyor belts are capable of running in refrigerated environments, which is ideal for cold storage and post-harvest cooling rooms.
- Chemical-resistant belts – Suitable for products or cleaning agents that may degrade standard materials.
- Static-dissipative belts – Important in powder handling or areas with sensitive electronics.
Different applications call for different belt properties. Belts used to handle food-grade products differ from those used in manufacturing or packaging and often fall into one or more of the following categories:
Choosing the wrong belt type can lead to faster wear or unsafe working conditions. Partnering with a manufacturer that understands your industry’s requirements can save you both time and money.
Mobius conveyors are designed for processors who need durable, food-grade solutions across a variety of industries. Choosing the right belt from the start can make cleaning and preventive maintenance easier and prevent higher long-term costs.
The Role of Automation and Technology
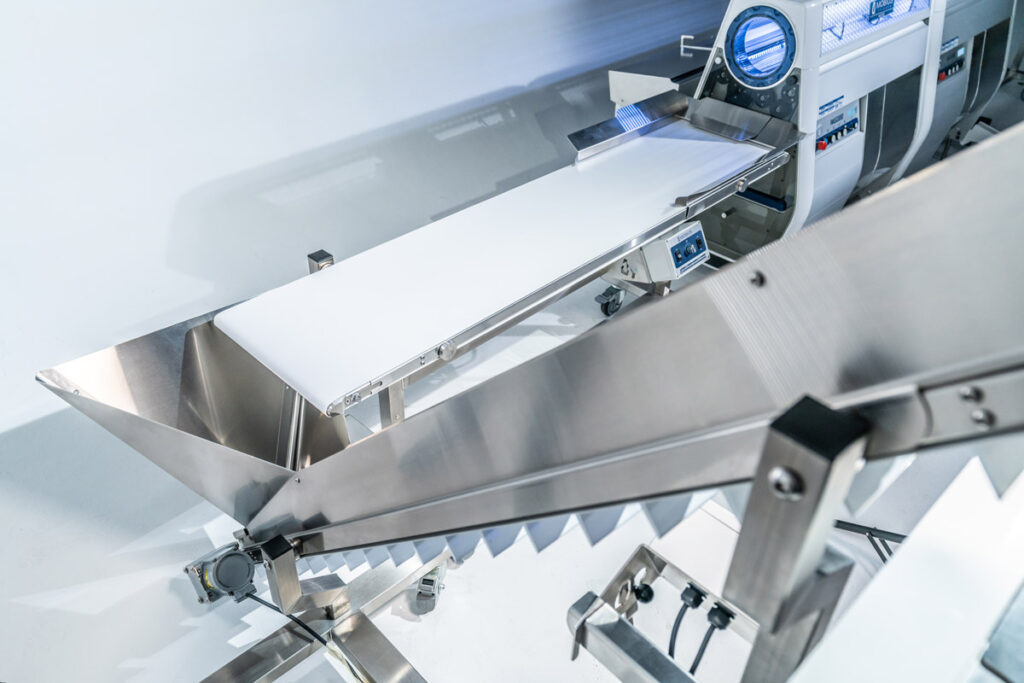
Modern facilities incorporate technology in a variety of ways to manage their conveyor equipment for conditions such as belt tension, motor temperature, and vibration in real-time.
These systems support predictive maintenance efforts and allow facilities to address issues before expensive failures occur. Predictive systems supplement human inspections and can flag subtle changes that human inspectors might miss, like motor current fluctuations or slight misalignments in bearings or
rollers.
Additionally, automated tracking systems can continuously adjust the belt’s position to maintain its alignment and prevent product spillage or wear on the belt’s edges. These automated systems reduce the need for manual adjustments and minimize operator error.
Mobius Food-Grade Conveyor Belt Systems
Conveyor belt maintenance is more than just a checklist item — it’s a strategic investment in your operation’s uptime, product quality, and compliance with regulations. A reliable conveyor system is the result of well-planned maintenance and choosing the right equipment for the job.
Preventive maintenance practices include routine inspections, sanitization protocols, and proper staff training. Whether you’re working with cannabis, cosmetics, or other agricultural processing, the fundamentals remain the same. Consistent care will extend equipment life and safeguard your operations.
Planning a facility upgrade or expansion? Our team can help. Explore the Mobius conveyor lineup or contact us to discuss your facility’s specific needs.
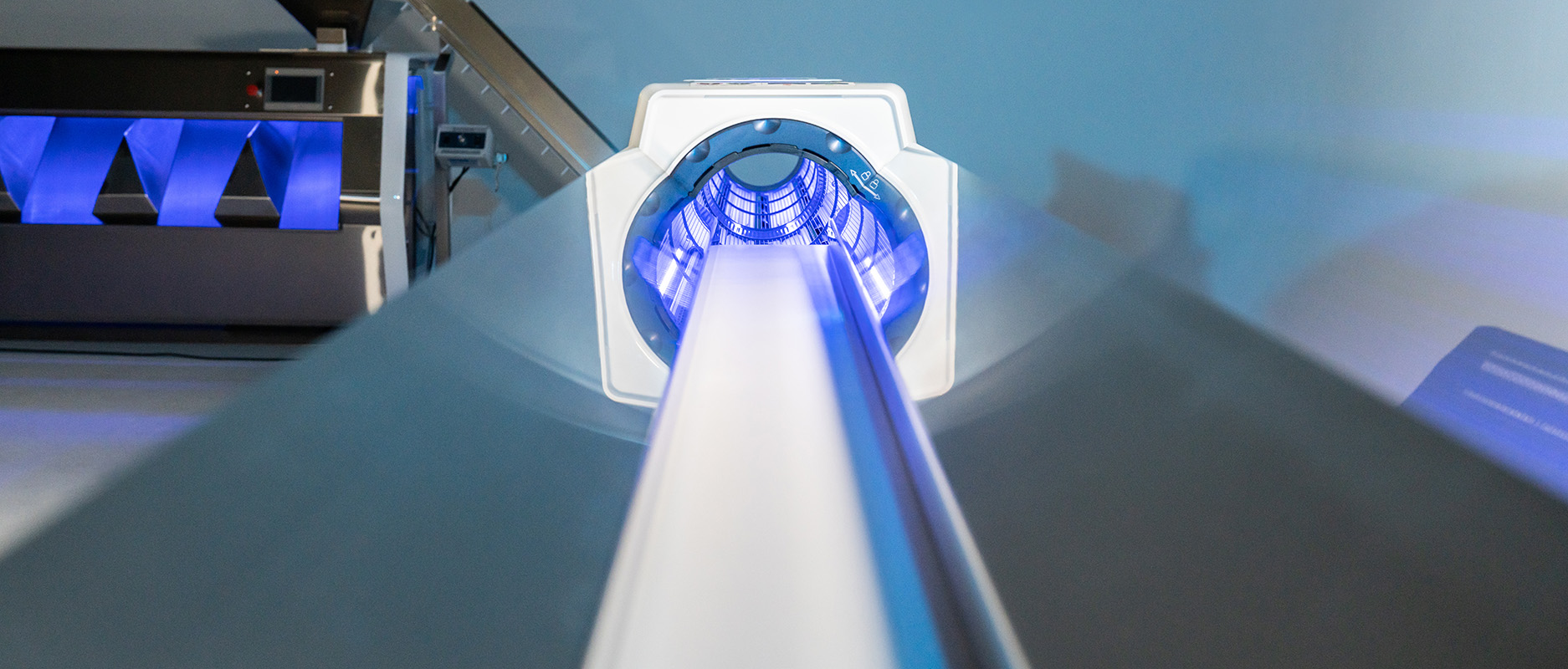
Mobius Conveyors
t